The horizontal boring and milling machining center, through the extension of the spindle and the rotation of the workbench, can carry out a variety of processing and is widely used in all walks of life. In recent years, in addition to the traditional versatility, high-power, high-speed, high-precision specifications are more required.
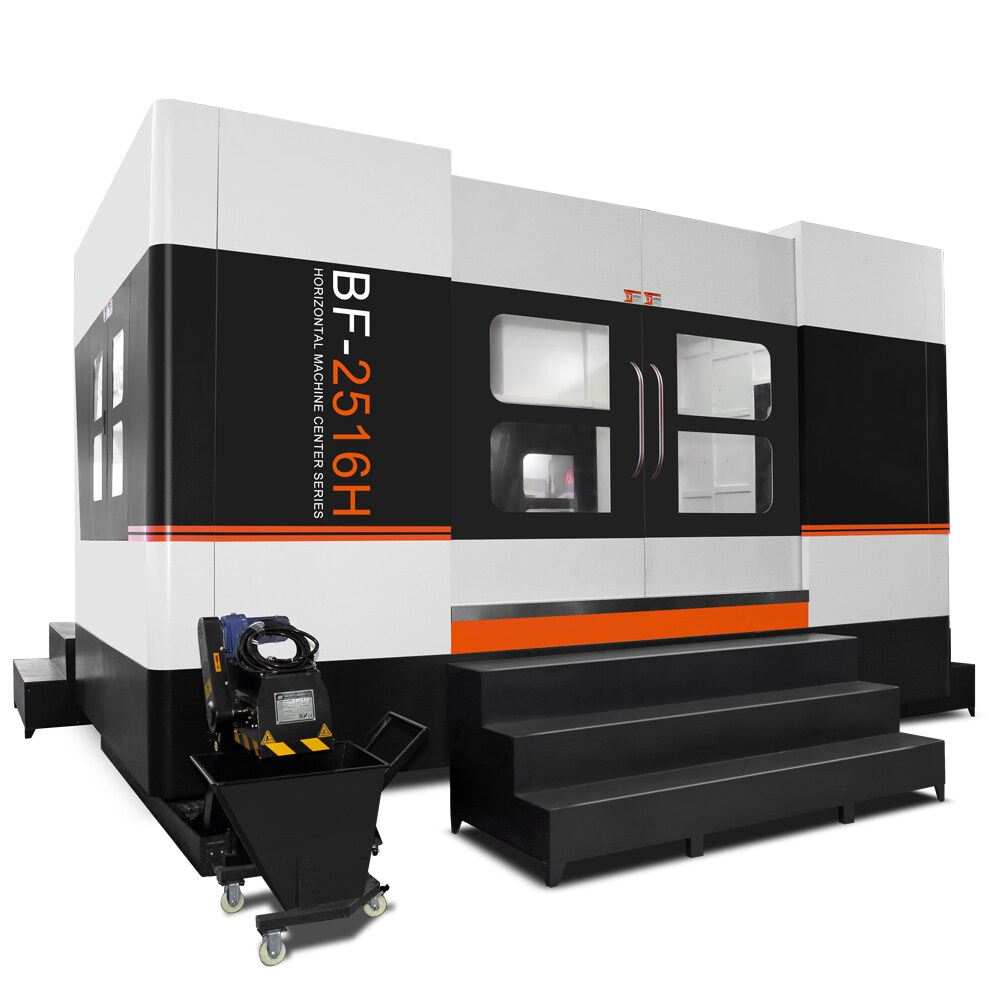
It has a wide processing range and is suitable for the end cutting of metal materials such as castings and steel parts. It can mill the two ends of ultra-long workpieces. This product is widely used in steel bridges, construction machinery manufacturing, shipbuilding, and other industries. 10. When the y and Z axes move, the spindle (W axis) expands and contracts, which is compatible with the spindle being closer to the workpiece and strong heavy cutting ability. Deep hole machining, which is usually prone to spindle drooping and vibration, and abnormal sound, can be free from the limitation of tool length if an extendable spindle is used. Large diameter spindles and bearings achieve high rigidity and sufficient heavy cutting capacity. The thick and strong spindle and large diameter bearing design realize high rigidity, and the lengthened bearing spacing ensures the spindle structure that can extend the length of the spindle.
Horizontal boring and milling machining center can not only boring but also milling, drilling, tapping, machining with NC plane milling disc, etc. it is a machine with many processing methods in machine tools.
Safety operation specification for horizontal boring and milling machining center
- The boring and milling machining center shall be managed and operated by a specially assigned person, who must undergo professional training and strictly abide by the safe operating procedures to ensure the safety of personnel and equipment.
- Do not move the machine tool at will until you are familiar with the structure, performance, operation method, and precautions of the machining center.
- After the machining center is powered on, check whether the switches, buttons, and keys are normal and flexible and whether the machine tool is abnormal; After entering the program, you should carefully check whether the code, address, numerical value, sign, decimal point, and syntax are normal; Measure and calculate the workpiece coordinate system correctly, and check the results obtained; Input the workpiece coordinate system, and carefully check the coordinates, coordinate values, signs and decimal points.
- During trial cutting and machining, after tool wear and tool replacement, re-measure the tool position and modify the tool compensation value and tool compensation number; After the procedure is modified, the modified part should be carefully checked.
- Before the operation, wear labor protection articles as required, and check whether the protective covers of all parts of the processing center are intact, whether the transmission parts are normal, and whether the lubrication systems are lubricated and changed regularly according to the instructions.
- Tools, fixtures, and workpieces must be firmly clamped, and tools and measuring tools must not be placed on the workbench.
- When clamping the workpiece, it should be handled with care to prevent bumping and damaging the worktable; When the workpiece is heavy, the bearing capacity of the machine tool workbench should also be verified, and overload operation is not allowed.
- When the milling and boring machining center is hoisted by a crane, it is necessary to prevent the collision between workpiece and equipment, and pay attention to personal safety.
- After starting the machine, check whether the machining center has various alarm information on the display, check the alarm information and eliminate the alarm in time, check whether the movement of the spindle and workbench in all directions is normal, and check whether the pressure indicator, tool change device, tool magazine device and peripheral equipment are normal.
- During the processing, the protective cover should be closed and the iron filings should not be removed. The machine must be shut down for loading, unloading, and measuring workpieces. During the operation of the processing center, the operator shall not leave the post without authorization, and the machine must be shut down if it is necessary to leave.
- The operation speed of the machining center is high. Before executing the operation instructions and automatic operation of the program, judge the correct line and operation results of the operation instructions and programs in advance, and then operate. The machining program should be strictly verified before being operated, to avoid accidents as much as possible.
- When cleaning iron filings, use certain tools, and be careful not to be scratched by chips. When there are too many iron filings in the chip chute, clean them manually first, and then turn on the chip conveyor.
- In case of abnormal noise or abnormality during the operation of the milling and boring machining center, stop the machine immediately, turn off the power supply, repair it in time, and make relevant records.
- After the work, turn off the power, remove the chips, wipe the machine tool, and add oil for lubrication; Clean and tidy up, truthfully fill in the mechanical point inspection form, and timely report any problems found.
Searching for a 3 axis horizontal milling machine, 5 axis horizontal milling machine, summit horizontal boring mill supplier, wholesaler, manufacturer from China, you can get high-quality products at a nice price.